Steel Manufacturing and the Circular Economy: Creating a More Sustainable Future
Manufacturing remains a core driver of the U.S. economy. Yet every day, concerns about the industry’s environmental impact grow. More manufacturers are taking a holistic view of sustainability in their products and operations. And the steel manufacturing industry is at the forefront of that reinvention.
Forward-looking steel manufacturing companies realize that embedding sustainability practices into how they do business isn’t just good for the planet. It can also fuel efficiencies, helping create a more resilient and competitive marketplace — and America — in the process. Plus, sustainable manufacturing practices have societal benefits, such as improving worker safety, reducing the amount of toxins released into the environment, and building trust and loyalty with customers and employees.
So how can companies implement innovative manufacturing technologies and approaches that support a circular economy, where waste is minimized, and resources are kept in use for as long as possible?
Less Waste, More Recyclability
Steel ranks as the most recycled material on the planet. Even after steel is manufactured, it’s continuously recyclable while maintaining the same level of quality. But companies like Zekelman Industries (ZI) have even more ambitious goals to reduce their environmental impact. ZI is taking steps to reduce waste during the manufacturing process and use less material overall in our products.
Case in point: Hollow structural sections (HSS), steel tubes with hollow cross-sections that produce less scrap than traditional steel manufacturing. With a high strength-to-weight ratio, HSS deliver exceptional structural support, which often means less total steel is required to do the job. The result? A lower carbon footprint—without a reduction in product quality. The lightweight yet strong steel tubing can be used as structural elements in the construction of bridges and buildings like airports and stadiums, as well as in a range of manufactured products.
Another way manufacturers are helping boost the circular economy is by adopting closed-loop cooling systems that don’t allow contact between the atmosphere and the cooling water. The cooling water is kept inside carbon-steel tubing and piping at all times, preventing it from being contaminated by outdoor air and increasing energy efficiency. Unlike with a traditional cooling tower, closed-loop systems don’t require additional water to replace what’s lost from evaporation. The water is continuously recycled during the manufacturing process. By incorporating these systems, ZI saves energy and optimizes costs through resource efficiency, among other sustainability benefits.
Leading manufacturers like ZI are finding ways to prioritize green manufacturing across their operations. Yet the biggest boost to sustainability may be domestic steel manufacturing itself. With low energy intensity and CO2 emissions per ton of steel produced, American steel ranks among the cleanest and most energy efficient of steel industries around the world, according to a report by Global Efficiency Intelligence.
From transportation to mining to construction, the U.S. steel industry supports almost 2 million jobs, generating over $520 billion in industry output. That said, as one of the largest energy consumers, the industry must also take responsibility for its impact on society and the environment by taking action to reduce energy consumption, air and water pollution, and carbon emissions.
The way forward for ZI? Continuing to roll out innovations to cut waste and minimize pollution, while capitalizing on low-carbon technology deployment and maximizing resource efficiency to maintain—and grow—a vibrant domestic steel industry.
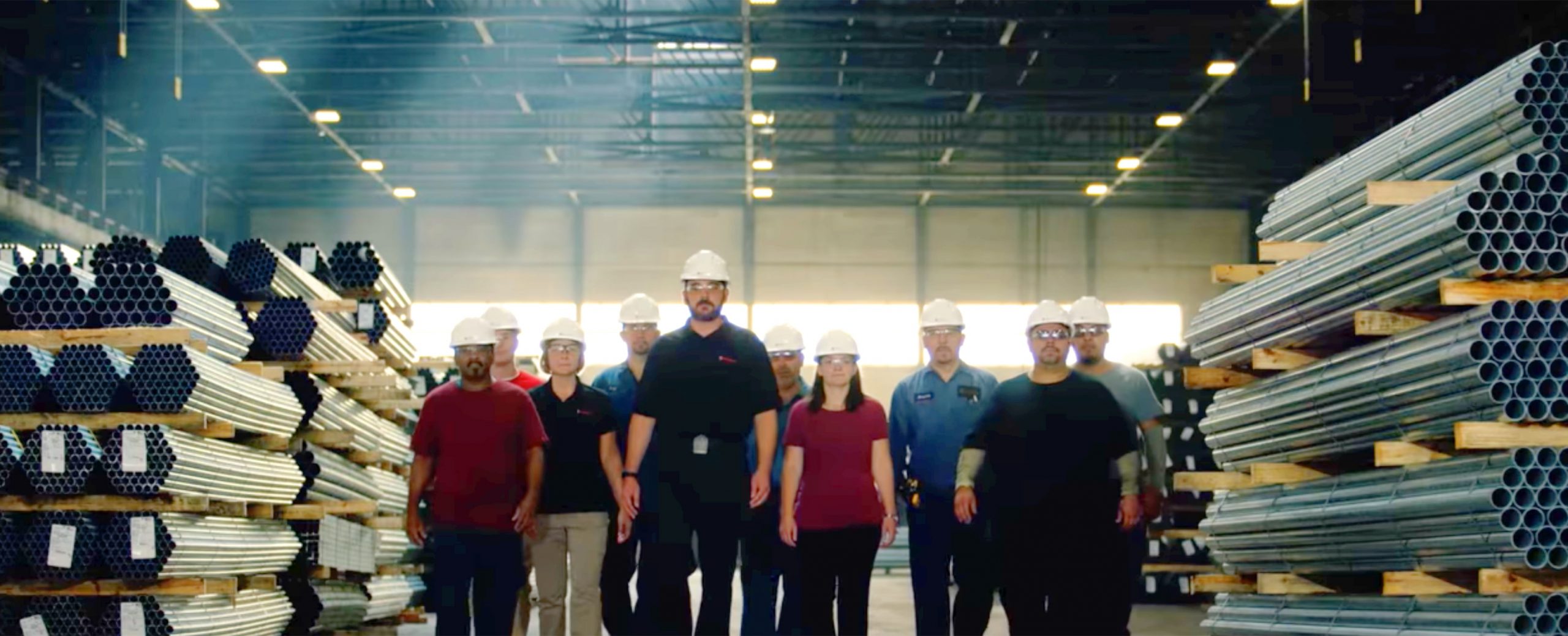
There’s nothing better than building something you believe in.
Zekelman companies are in constant motion, expanding our teams and challenging convention.
"*" indicates required fields