Making Safety a Priority: 5 Ways the Manufacturing Industry Can Protect Workers
Considerable progress has been made in factory safety thanks to developing technologies and preventive measures, but there’s always work to be done. Companies like Zekelman Industries (ZI) recognize that and have made teammate safety and well-being a top priority.
“Safety at Zekelman is more than just words. It’s the beginning of every meeting. It’s the beginning of every day,” says Dave Campbell, plant manager for Wheatland Tube in Wheatland, Pennsylvania. “It’s always part of what we’re doing.”
Here are five ways today’s manufacturers can prioritize worker safety.
1. Invest in automation.
Automating factory operations reduces human error and improves overall system productivity to create — and maintain — a safer work environment. Workers can oversee potentially dangerous machines and equipment operations while keeping a safe distance.
“It creates a less stressful environment,” says Brad England, a machine operator at the Wheatland/Western Tube facility in Rochelle, Illinois. “You’re safer. It’s easier on the body.”
2. Incorporate robotics.
Like automation, the use of new robotic technologies improves teammate safety by allowing them to perform tasks that usually carry risk, such as moving heavy products using forklifts.
Rather than eliminating jobs, robots actually help employees retain roles by improving factory efficiency and protecting workers. “It keeps me safer,” says England, who works with robots daily on the Rochelle factory floor. “It lets me go home at the end of the day the way I came in.”
3. Apply artificial intelligence.
The rise of artificial intelligence (AI) is also changing the landscape of worker safety. In 2020, ZI partnered with Everguard.ai to use AI and sensor fusion to increase safety measures at steel facilities. Everguard’s Sentri360™ platform was brought to Zekelman’s Atlas Tube facility in Blytheville, Arkansas, as a proactive approach to help prevent workplace injuries and accidents.
Initial efforts have focused on using AI and computer vision to enhance safety protocols for logistics and the tarping of trucks in the facility’s shipping bays. “This innovative new AI platform has the potential to further assist us in operating at the highest possible level of safety and efficiency,” says Barry Zekelman, executive chairman and CEO.
4. Install machine guards.
Probably one of the simplest initiatives is to install machine guards to protect workers against potential injuries by creating physical barriers to prevent an operator from having any body part within the “danger zone” while a machine is in operation, according to the University of California, Santa Barbara.
Nikki Jaggers, a pipe tester operator for Wheatland Tube, has seen the benefit of these guards firsthand. “If you wanted to go inside my machine, for example, you would have to turn the gate off, put a lock on it, and then enter into where the machine is,” she says.
5. Provide in-depth training.
Ultimately, continual training is the first step and perhaps the most important way companies can prioritize worker safety. That means creating an environment where safety training is both ongoing—and mandatory—for all employees and visitors. The value of safety must be emphasized and supported at all levels.
Alexis Lopez, a Wheatland/Western Tube manager, plant training and quality, oversees the training of new employees on the factory floor. “[This job] has given me the opportunity to be hands-on and lead the new generation of our workforce,” says Lopez. “It has enabled me to help them with their training. It has helped me better understand the equipment. It has helped me also better understand the mindset of the new workforce coming in.”
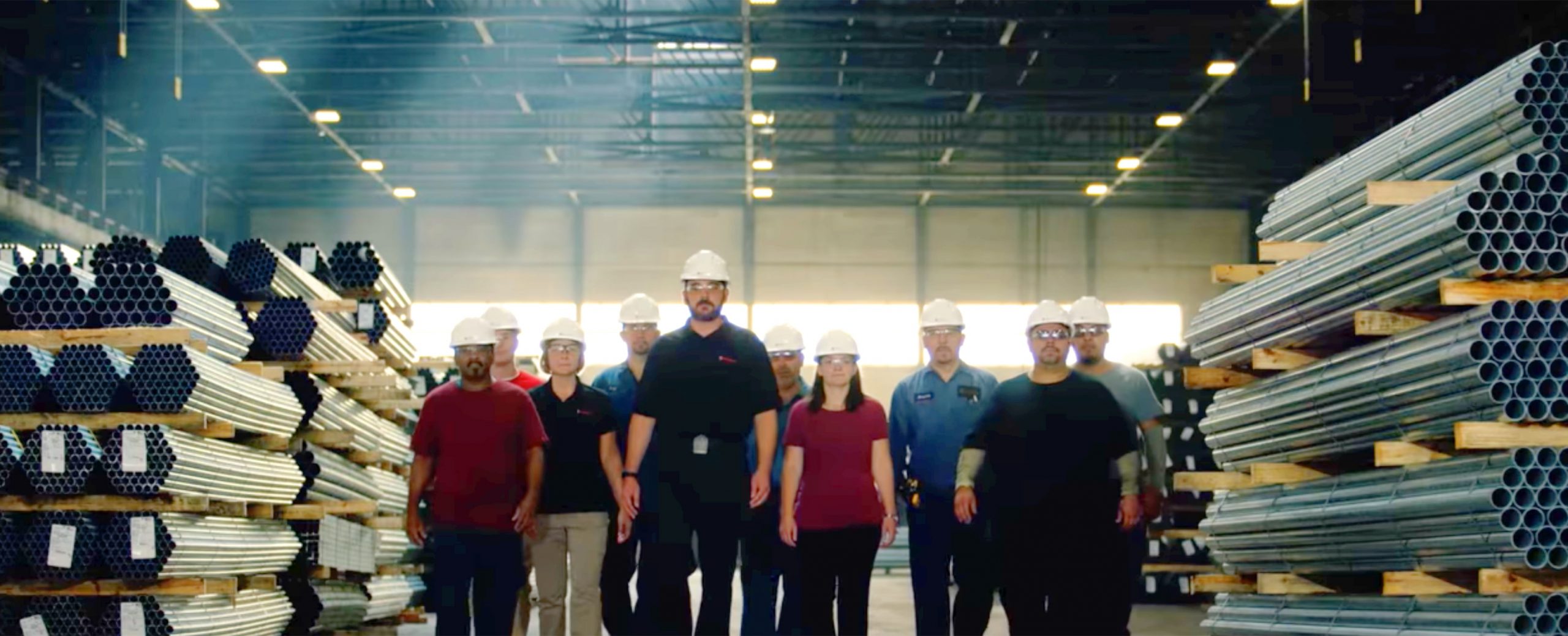
There’s nothing better than building something you believe in.
Zekelman companies are in constant motion, expanding our teams and challenging convention.
"*" indicates required fields