A Greener Blueprint: The Case for Using American-Made Steel in Your Construction Projects
In the competitive construction sector, savvy contractors and builders know that the best structures are made using the best materials. But there’s another legacy you leave with the materials you choose: their impact on the environment and communities.
Cost is a chief factor project teams must consider when sourcing construction materials. However, upfront costs can be remarkably deceptive. Where steel comes from and how it’s made can significantly affect quality, availability, sustainability, and the economic impact on local communities. In reality, choosing “cheaper” foreign steel components can lead to issues ranging from higher transportation costs and supply chain delays to a larger carbon footprint for your project. Transporting steel via cargo ship, for example, is harmful to the environment. In 2022, there were an estimated 945.8 million tons (858 million tonnes) of CO2 emissions globally from the shipping industry, compared with 814.6 million tons (739 million tonnes) of CO2 emissions from air travel, according to the Organization for Economic Co-operation and Development (OECD).
“When you have a ton of steel made in the U.S. versus a ton of the steel made in India or in China, the environmental impact of that is much less,” explains Mickey McNamara, President, Z Modular and Executive Vice President of Zekelman Industries. “The carbon footprint of that is much less.”
Assessing Material Quality and Sustainability
Despite obvious similarities, foreign steel and U.S. steel are very different material choices. Domestically manufactured steel is subject to stricter manufacturing standards and strong regulatory controls. It’s also highly durable and recyclable. In North America, “standards are much higher than they are any other place in the world,” McNamara says.
For example, the emissions of hot-rolled structural steel sections (HSS) produced in China emit three times more greenhouse gas than equivalent sections produced in the U.S, according to Atlas Tube, a Zekelman Industries company. So manufacturing these domestic steel products produces 60% less greenhouse gas with zero wastewater.
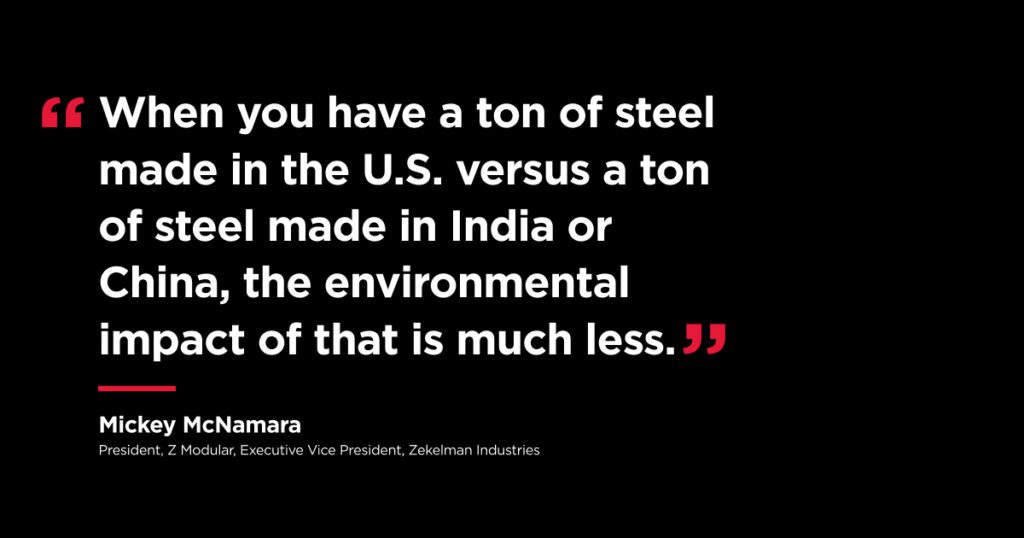
The result? Better products and projects—and opportunities for construction companies and project teams to level up sustainability. That’s a core focus for McNamara and his team at Z Modular, a Zekelman company that provides modular building and construction services. “All of the components of our buildings, we look at it the same way: ‘How do you have the smallest environmental footprint?’” he says. “The simplest way is to do it domestically.”
Sourcing cheap steel also comes at a greater cost to our planet, explains Barry Zekelman, Executive Chairman and CEO of Zekelman Industries. Foreign steel producers generate exponentially more CO2 emissions due to using dirtier coal production with less environmental regulation. Choosing foreign steel also means transporting steel over long distances—adding to its carbon footprint. “Cheap isn’t cheap,” Zekelman says. “There’s a price to pay. The environment is paying the price.”
Steel manufactured in North America typically contains 90% or more recycled steel, resulting in 75% less emitted CO2 than traditional manufacturing methods.
These issues become even more problematic when you consider that steel is by nature, a green material. The American Iron and Steel Institute reports that steel manufactured in North America typically contains 90% or more recycled steel, emitting 75% less CO2 than traditional manufacturing methods. What’s more, this steel can be repeatedly recycled and remade without compromising quality.
Reinforcing the Benefits of Domestic Steel
While initial material cost is a consideration for construction teams and contractors, the long-term value of material choices—along with client and public perception—is paramount. Whether you’re aiming to optimize costs or build a more sustainable business model, taking a closer look at material selection and sourcing practices is always worthwhile.
Remember: The true cost of steel products for construction encompasses more than the purchase price. Domestic steel is an all-around smart and sustainable choice for structures because it promotes a circular economy that reduces waste, lowers emissions, streamlines the supply chain, and conserves valuable resources. The decision to use domestic steel may also encourage public support for clean energy projects, such as solar assemblies and green buildings while supporting local economies and job creation. The U.S. structural steel industry alone provides 115,000 direct jobs and hundreds of thousands of indirect jobs, according to the American Institute of Steel Construction.
It benefits communities, too. According to Zekelman estimates, purchases of U.S.-produced steel generate tax revenue of about $500 to $600 per ton of steel pipe and tube sold. That money goes directly back into the economy at the federal, state, and local levels.
“The reality is that things built in North America are done in a more socially conscious way,” McNamara says. “The workers are treated better; the environment is treated better. Our standards are much higher than any other place in the world.”
So, is it time to reconsider where your steel comes from?
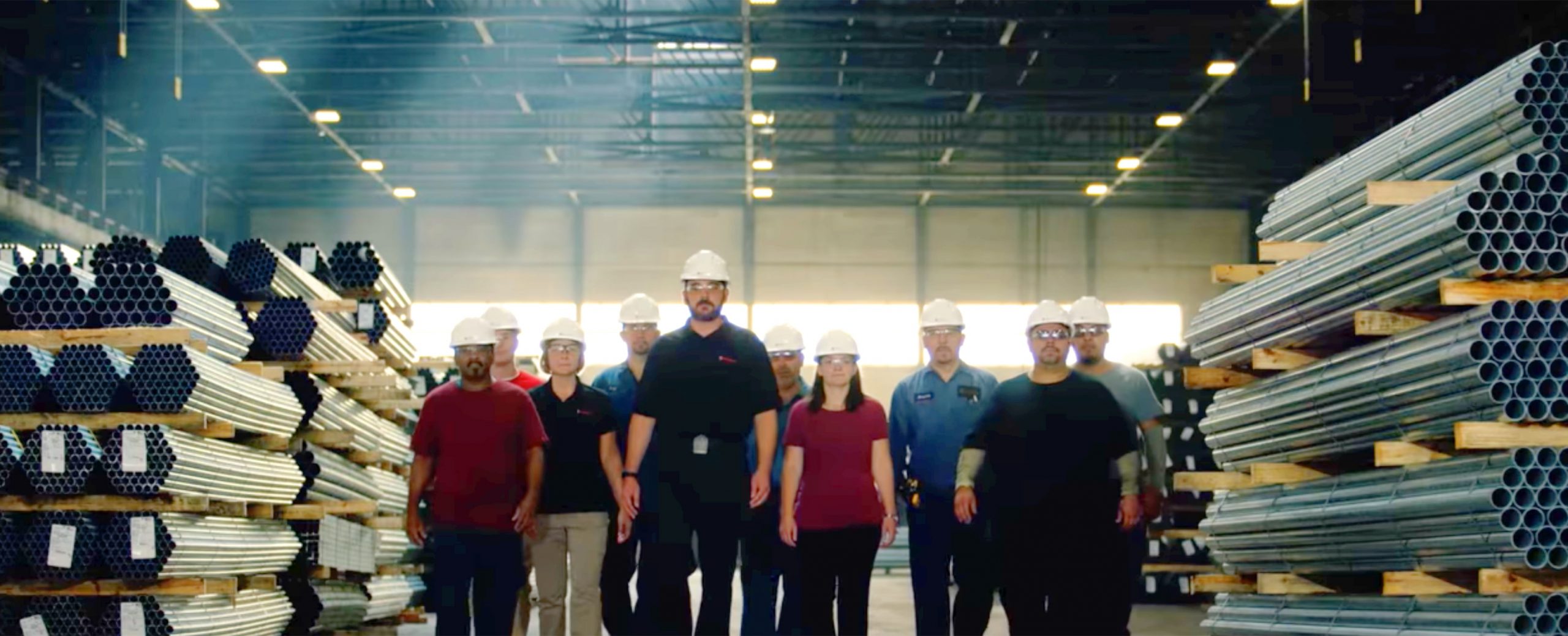
There’s nothing better than building something you believe in.
Zekelman companies are in constant motion, expanding our teams and challenging convention.
"*" indicates required fields